Sustainable circular solutions
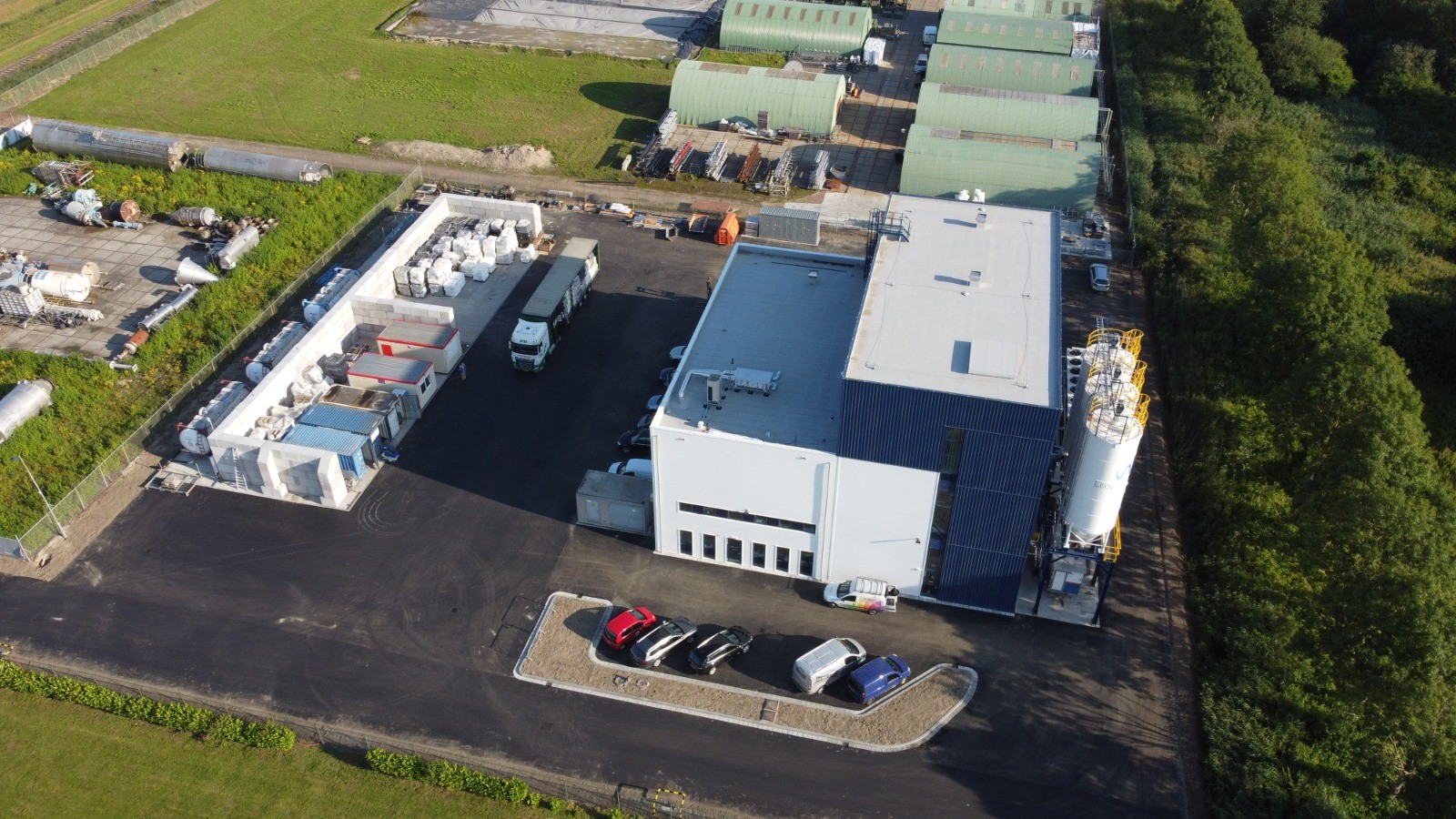
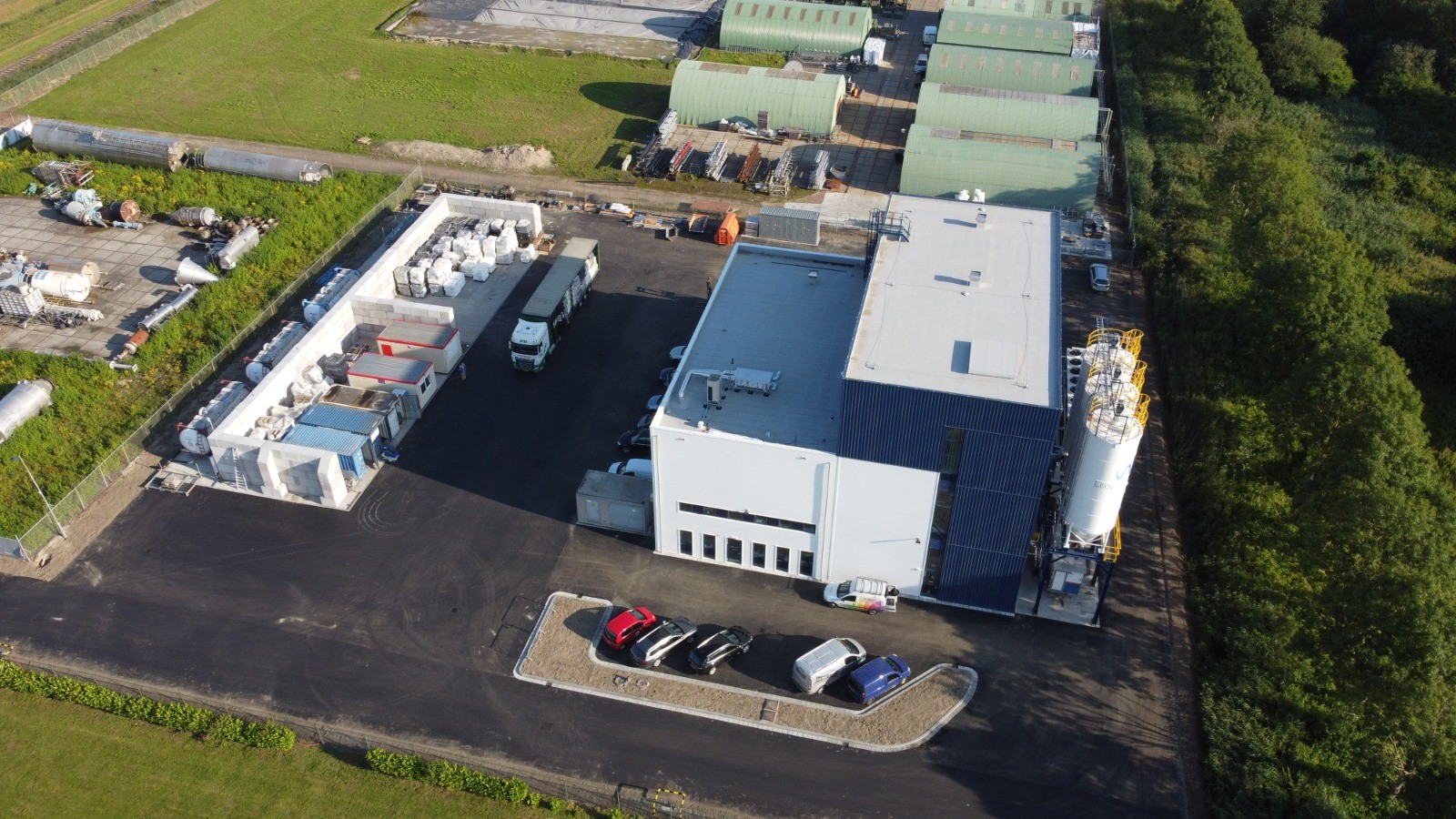
Consultancy and support for value chain cooperation & application of sustainable processes & materials
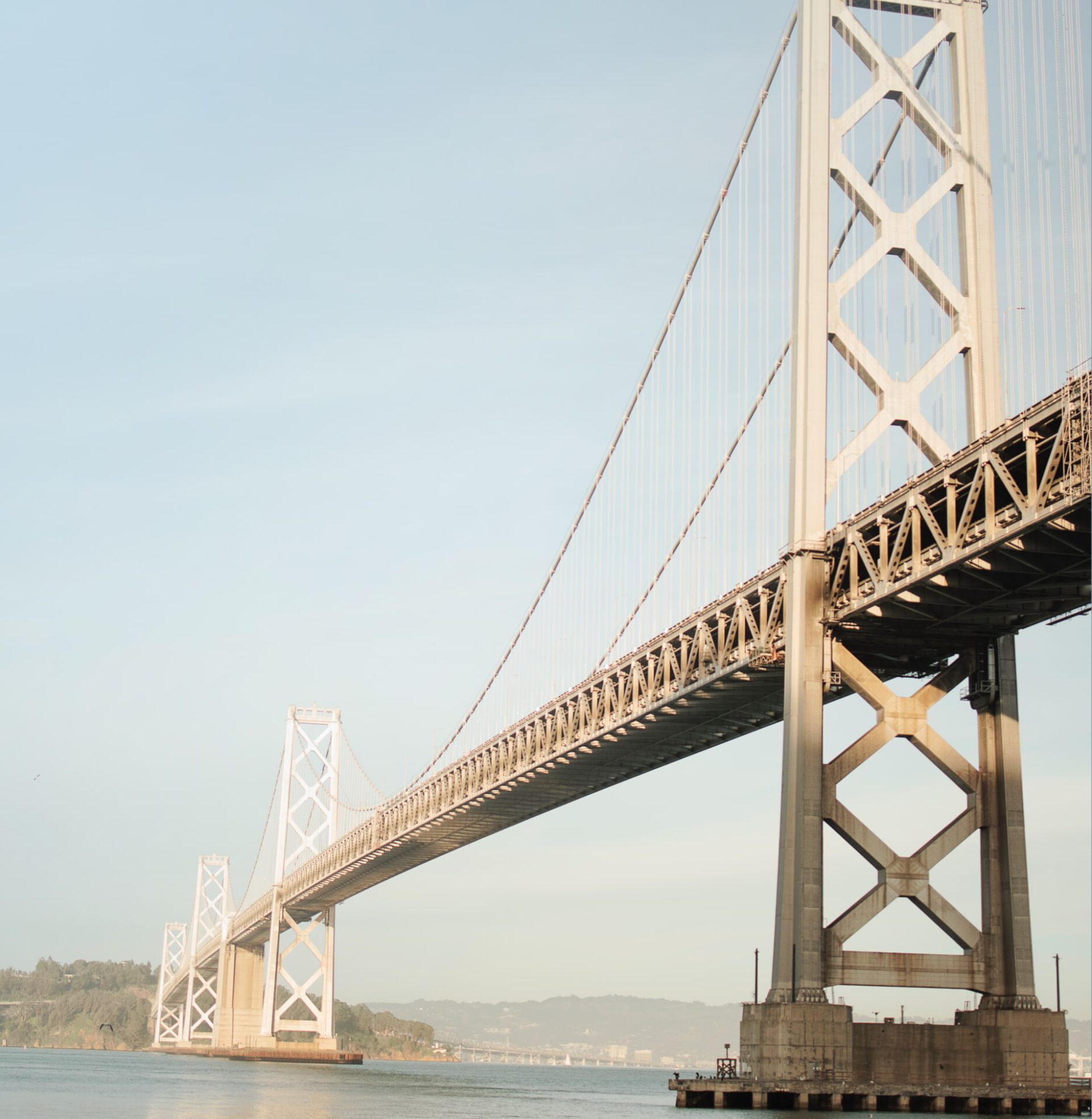
Users in the (foam) industry often face questions or have issues and detailed question that need answering: In general the (EPS) foam industry has three main challenges Circularity, Fire safety and Sustainability.
NEWS May 1st 2024 Formal start of Project BRAVE
Biologisch Recyclebaar Alternatief voor Verpakken met EPS (Biologically Recyclable Alternative to Packaging with EPS )
European and regional contribution for a biologically recyclable alternative to EPS
A biobased and biodegradable alternative to EPS (expanded polystyrene) packaging materials based on starch foam. With a new process technology, companies from Barneveld, Doorn, Ede and Enschede in the Netherlands will start working towards the goal of developing a sustainable alternative for packaging products heavier than 5 kilos. This alternative is recyclable, just like paper, but can also be composted.
Products, such as heating and ventilation equipment, furniture and white and brown goods, are currently packaged with fillers and corner pieces based on expanded polystyrene (EPS). There is an increasing need in the market for alternatives. Not only because legal restrictions are imposed in some parts pf the world, but also because companies and consumers demand to have a choice . The material to be developed by the project partners must have comparable properties to EPS with regard to density, resilience, tensile and bending strength, but with a low carbon footprint.
The consortium consists is led by Paperfoam B.V. and consists of the following five partners: PaperFoam B.V. from Barneveld, Innograaf B.V. from Doorn, Thermoware Particle Foam Machinery B.V from Barneveld, Jadima Fijnmetaalwerking from Ede and Vaventis from Enschede. Together they receive a subsidy of €583,538 from the European Regional Development Fund (ERDF), with co-financing from the province of Gelderland and Overijssel. The total investment costs amount to € 1,167,077.
The entrepreneurs have submitted a subsidy application for the project to the European Fund for Regional Development in the East of the Netherlands https://www.efro-oost.eu/nieuws/europese-bijdrage-voor-vier-duurzame-innovaties-in-oost-nederland
The contribution is a subsidy for test and demonstration projects. This subsidy is intended for testing new applications and solutions from SME’s, so that innovations can be brought to the market more quickly. Innovations are important for the competitive position of companies and therefore for the regional economy. EFRO OOST is a European subsidy program to which the Ministry of Economic Affairs and Climate Policy and the provinces of Gelderland and Overijssel also contribute. Helga Witjes, deputy for Economy & Innovation of the province of Gelderland: “For an increasing number of companies in our province, circular working is no longer a future but an everyday practice. They know this is the only way forward. They earn money and create new jobs with circular innovations.”
NEWS Non spreading, non floating, microplastic free biodegradable infill meets FIFA standards
New legislation drawn up by ECHA since the introduction of EU Regulation 2023/2055 of 25 September 2023 restricts the formation of microplastics. This is particularly relevant for the infill used on artificial grass football pitches.
Ground SBR infill, derived from ground car tyres, gives rise to a multitude of environmental problems such as the smell of butadiene and the leaching of PAHs and zinc. Non-infill pitches that last a few months are not a good solution and the use of rubber substitutes such as TPE or TPU ultimately still lead to the formation of microplastics.
The industry has tried to develop biodegradable infill. For example; cork, redwood chips and olive pits, all of which pulverise too quickly or cause skin problems during sliding. PLA foam and PBAT foam with densities of 200-300 kg/m3 offer a good alternative, but can float on the field and still contribute to the formation of microplastics, because they do not degrade quickly enough and do not comply with ECHA legislation.
Coated sand has been used for a long time that was coated with polyethylene. It provides an elastic substrate, offers excellent playability and this solved many problems, such as spreading over the field and taking the infill home, but ultimately it is not a microplastic-free solution.
Together with a Finnish company Saltex Oy, Innograaf has developed and patented the infill based on a cellulose polymer that does not lead to the formation of microplastics, because it does not in the “desert climate” on the field, but does outside the field.
The product performs very well during its lifespan on the field, because certain environmental aspects are missing to give a fast degradation during use. However, once the material comes into contact with fungi in the soil or comes into prolonged contact with salt or fresh water, it does break down.
Combined with the relatively low cost compared to other biobased alternatives, it delivers excellent performance, as shown by the experiences of players, and it meets FIFA standards. In Scandinavia, 40 fields are already equipped with this infill. In the Netherlands, it is unknown.
Microplastic-free infill is now available for use on football fields, allowing young children to play on the field without the risk of skin damage and the infill does not come home with you, does not end up in the washing machine and does not end up in the environment.
https://saltex.eu/saltex-bioflex-eco
Technical questions
Sustainability